How To Ensure Quality Control Effectively For Manufacturing Top-Notch Garments
A single subpar garment can tarnish a brand's reputation and lead to lost customers. That's why rigorous quality control is essential throughout the apparel production process.
Huzaifa khatri
2/13/20252 min read
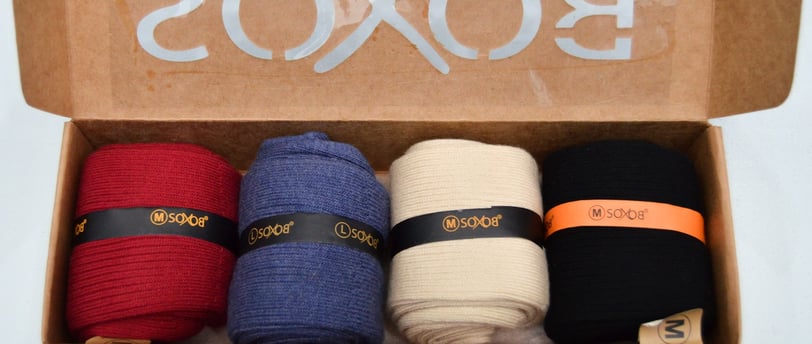
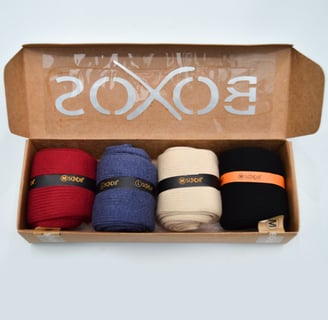
In the competitive world of fashion, quality is paramount. A single subpar garment can tarnish a brand's reputation and lead to lost customers. That's why rigorous quality control is essential throughout the apparel production process. At [Your Company Name], we specialize in providing comprehensive inspection services that help brands maintain the highest quality standards, ensuring their garments are top-notch.
Why is Quality Control So Important?
Quality control isn't just about catching defects; it's about building trust with your customers. Consistent quality demonstrates your commitment to excellence and reinforces your brand's value. Effective quality control can also
Reduce returns and refunds: By identifying and addressing quality issues early on, you can minimize the number of returned or refunded items, saving your business time and money.
Protect your brand reputation: High-quality garments enhance your brand image and foster customer loyalty. Conversely, poor quality can lead to negative reviews and damage your reputation.
Optimize production efficiency: Identifying quality issues during the production process allows you to make corrections quickly, preventing larger problems down the line and streamlining your operations.
Ensure compliance with regulations: Many countries have strict regulations regarding garment safety and quality. Thorough quality control helps you ensure compliance and avoid costly penalties.
Our Inspection Services: A Closer Look
At [Your Company Name], we offer a range of inspection services tailored to our clients' specific needs. Our experienced inspectors meticulously examine garments at various stages of production, from raw materials to finished products. Our services include:
Fabric Inspection: We assess fabric quality, checking for defects, color variations, and adherence to specifications.
Pre-Production Inspection: We evaluate samples and patterns to ensure they meet design requirements and identify any potential production issues.
Inline Inspection: During the manufacturing process, we conduct regular inspections to catch any defects early on and prevent them from becoming widespread.
Final Inspection: Before garments are shipped, we perform a thorough final inspection to ensure that they meet all quality standards.
Container Loading Inspection: We oversee the loading of containers to ensure that the garments are properly packed and protected during transit.
Tips for Brands: Implementing Effective Quality Control
Even if you partner with a third-party inspection company, it's essential for brands to have their own internal quality control processes in place. Here are a few tips:
Develop clear quality standards: Establish detailed specifications for your garments, including acceptable defect levels and tolerances.
Train your staff: Ensure that your production team is well-trained in quality control procedures and understands your standards.
Conduct regular inspections: Implement regular inspections at every stage of the production process, from raw materials to finished goods.
Document everything: Maintain detailed records of your inspections, including any defects found and corrective actions taken.
Communicate with your suppliers: Establish open communication with your suppliers and work collaboratively to address any quality issues.
Avoiding Common Pitfalls
Many brands encounter common pitfalls when it comes to quality control. Here are a few to avoid:
Relying solely on final inspection: Catching defects early on is crucial. Don't wait until the final stage to identify problems.
Cutting corners on inspections: Thorough inspections take time and resources, but they're essential for ensuring quality.
Lack of communication: Poor communication between your team, your suppliers, and your inspection company can lead to misunderstandings and quality issues.
Inadequate training: Without proper training, your staff may miss critical defects or not understand how to implement quality control procedures effectively.
Partner with Texcelence for Quality Assurance
At Texcelence, we're committed to helping brands deliver top-notch garments. Our comprehensive inspection services and expertise in quality control provide you with the assurance you need to protect your brand reputation and build customer loyalty. Contact us today to learn more about how we can help you achieve your quality control goals.